Requirements (Education, experience, competencies and specific job requirements):
Education / Certification:
- Bachelor of Chemical / Bachelor of Technology in Chemical Engineering or Diploma / Master of Science in Polymer Technology.
Experience and Skills:
- Minimum 5 to 10 years of experience in industry related to Batch operations, compounding –preferably solid / powder material handling.
- Good knowledge of continuous / semi-continuous process plant.
- Familiarity with ISO 9001, NSF, 5S systems (documentation, implementation, and compliance).
- Well versatile in best HSES practices, Knowledge of process safety.
- Should have experience of 5S, Lean Management, Operation excellence, RCA (Route Cause Analysis), Risk assessment and Permit systems.
- Experience of operating PLC (Programmable Logic Controller), SCADA (Supervisory Control And Data Acquisition), DCS (Distributed Control System) and various automation system in process industries.
- Desire & aptitude to be leader.
- Good experience of managing in multi-shift environment in an MNC will be an added advantage.
- Experience of recording the DATA in SAP.
- Good verbal and written communication in English.
- Computer Skills: MS Office.
TO apply click on APPLY now
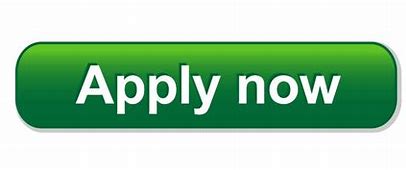
Tips for Chemical Engineers: Becoming an Effective Shift-In-Charge
As a shift-in-charge in a chemical engineering environment, you hold a pivotal role in overseeing operations, ensuring safety, and leading your team. Here are comprehensive tips to excel in this role, tailored for those looking to advance their careers in chemical engineering.
1. Technical Proficiency in Chemical Processes
- In-Depth Knowledge of Chemical Processes: Master the chemical processes and technologies in your plant. Familiarize yourself with equipment, process flows, and the chemical reactions involved. Stay updated with the latest advancements by attending industry conferences, participating in webinars, and reviewing technical journals. Understanding the intricacies of the processes allows for better decision-making and troubleshooting.
- Implement Safety Protocols: Prioritize safety by adhering to protocols, conducting regular safety drills, and understanding Material Safety Data Sheets (MSDS). Ensure all team members use appropriate personal protective equipment (PPE) and are trained in emergency response. Implement a robust safety training program that includes scenario-based training and regular refreshers. Promote a culture of safety by encouraging team members to report near-misses and potential hazards.
- Advanced Problem-Solving Skills: Develop a systematic approach to troubleshoot issues, using tools like Fishbone diagrams, Failure Mode and Effects Analysis (FMEA), and Root Cause Analysis (RCA). Implement corrective actions promptly to minimize downtime and maintain process efficiency. Foster a problem-solving mindset within your team by involving them in brainstorming sessions and solution development. Utilize data analytics to identify trends and predict potential issues before they escalate.
2. Leadership and Team Management
- Effective Team Management: Lead a diverse team with strong interpersonal skills. Recognize individual strengths, provide regular feedback, and resolve conflicts efficiently. Set clear goals and facilitate regular team meetings to align efforts. Encourage open communication and create an inclusive environment where all team members feel valued and heard. Implement team-building activities to strengthen relationships and improve collaboration.
- Strategic Delegation: Delegate tasks based on team members’ skills, ensuring efficient workload management. Provide clear instructions and necessary resources, while monitoring progress to ensure high standards are met. Utilize a project management tool to track tasks and deadlines. Offer mentorship and guidance to team members taking on new responsibilities, helping them develop their skills and confidence.
- Continuous Training and Development: Identify training needs and organize sessions to enhance technical skills, safety knowledge, and soft skills. Offer cross-training opportunities to broaden team members’ expertise, making the team more versatile and resilient. Encourage team members to pursue certifications and continuous education to keep pace with industry standards. Establish a learning culture by providing access to online courses, industry publications, and professional networks.
3. Clear Communication and Reporting
- Clear Instructions and SOPs: Communicate instructions effectively, especially in complex or emergency situations. Utilize visual aids like flowcharts, diagrams, and written Standard Operating Procedures (SOPs) to ensure clarity. Regularly update SOPs to reflect any changes in processes or equipment. Conduct communication training sessions to improve the clarity and effectiveness of both written and verbal instructions.
- Detailed Reporting: Maintain accurate records of all shift activities, including production data, equipment status, incidents, and corrective actions taken. Prepare comprehensive reports for seamless handovers and informed decision-making. Implement a digital reporting system to streamline data collection and analysis. Use these reports to identify areas for improvement and to track progress toward operational goals.
- Constructive Feedback: Foster a culture of open feedback by holding regular performance reviews and one-on-one meetings. Provide specific, actionable feedback to help team members improve their performance. Recognize achievements and contributions to motivate and engage the team. Encourage team members to give feedback to you as a leader, fostering mutual respect and continuous improvement.
4. Optimizing Operational Efficiency
- Monitor Key Performance Indicators (KPIs): Track KPIs like production rates, yield, quality, and downtime. Use real-time monitoring and data analytics to identify deviations and optimize processes. Implement a dashboard system for real-time monitoring and alerts. Regularly review KPIs with the team to identify trends, set new targets, and develop strategies for improvement.
- Efficient Resource Management: Plan and allocate resources efficiently, including raw materials, energy, and labor. Optimize processes to reduce waste and improve energy efficiency, contributing to cost savings and sustainability. Conduct regular audits to identify areas where resources can be conserved. Implement energy-saving technologies and practices, such as energy-efficient lighting and machinery.
- Foster a Culture of Continuous Improvement: Implement lean manufacturing principles such as 5S, Kaizen, and value stream mapping. Encourage team input for process improvements and recognize valuable contributions. Create a suggestion system where team members can submit ideas for improving efficiency and safety. Celebrate successful improvements to reinforce the value of continuous innovation.
5. Prioritizing Safety and Compliance
- Safety as a Core Value: Embed a safety-first mindset in all operations. Conduct regular audits, risk assessments, and emergency drills. Stay informed about the latest safety regulations and best practices. Develop and maintain a comprehensive safety management system that includes hazard identification, risk assessment, and incident investigation. Promote safety leadership by setting a positive example and holding everyone accountable for safe behaviors.
- Ensuring Regulatory Compliance: Adhere to environmental regulations, occupational health and safety standards, and industry-specific guidelines. Address non-compliance issues promptly and prevent future occurrences through systematic improvements. Establish a compliance calendar to track deadlines for regulatory submissions and inspections. Work closely with regulatory bodies and stay updated on changes in laws and standards.
6. Adaptability and Stress Management
- Embrace Adaptability: Stay flexible and adaptable in a dynamic work environment. Manage unexpected issues effectively, adjusting plans and priorities as needed. Develop contingency plans for various scenarios, such as equipment failures or supply chain disruptions. Encourage a flexible mindset within your team, promoting agility in response to changes.
- Manage Stress Effectively: Develop stress management techniques, including regular exercise, mindfulness, and time management. Encourage team members to maintain a healthy work-life balance and provide resources for managing stress. Organize workshops on stress management and resilience. Create a supportive work environment where team members feel comfortable discussing stressors and seeking support.
7. Documentation and Data Analysis
- Accurate Documentation: Keep detailed records of operations, maintenance activities, and incidents. Proper documentation is crucial for audits, troubleshooting, and process optimization. Implement a document management system to ensure easy access and retrieval of records. Train team members on the importance of accurate documentation and compliance with data management policies.
- Leverage Data Analysis: Use data analytics tools to analyze shift logs, production reports, and other relevant data. Identify trends, optimize operations, and make informed decisions based on data-driven insights. Invest in advanced analytics software that offers predictive analytics and real-time monitoring. Use data insights to support continuous improvement initiatives and strategic planning.
8. Collaboration and Coordination
- Enhance Cross-Departmental Coordination: Collaborate effectively with other departments, such as maintenance, quality control, logistics, and procurement. Establish communication channels for issue resolution and goal alignment. Hold regular inter-departmental meetings to discuss operational challenges and opportunities. Use collaboration tools to facilitate information sharing and project tracking.
- Communicate with Management: Maintain regular communication with upper management. Provide detailed reports, participate in meetings, and present data-driven insights to secure necessary resources and support. Develop strong relationships with key stakeholders and decision-makers. Present achievements and challenges transparently, and seek feedback for continuous improvement.
Conclusion
Excelling as a shift-in-charge in chemical engineering requires a blend of technical expertise, leadership, and effective communication. By focusing on these key areas, you can lead your team to success, ensuring safe and efficient plant operations. This comprehensive approach not only enhances productivity but also fosters a positive work environment and a culture of continuous improvement.
Join our WhatsApp Grop:
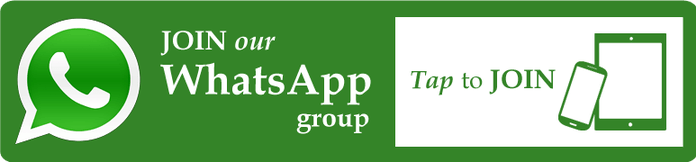